Coating Thickness Measurement solutions
Nextagen Analytics
2/3/20253 min read
How is Coating Thickness Measured?
Coating thickness measurement is a critical factor in ensuring product quality, process control, and cost efficiency across various industries, including manufacturing, construction, automotive, aerospace, and industrial coatings. Choosing the right method for measuring paint thickness, powder coatings, and other surface finishes can have a significant impact on durability, performance, and regulatory compliance.
This article explores various techniques for measuring coating thickness, including nondestructive and destructive testing methods, while addressing their applications, advantages, and limitations.
Why is Coating Thickness Measurement Important?
The thickness of a coating, film, or protective layer plays a crucial role in determining its performance, longevity, and adherence to industry standards. Key reasons why coating thickness measurement is essential include:
Quality Control – Ensuring coatings meet specified thickness levels to provide adequate protection and performance.
Process Control – Maintaining consistent film application reduces material waste and improves efficiency.
Cost Control – Applying coatings that are too thick wastes material, while undercoating can lead to premature failure.
Regulatory Compliance – Many industries, including automotive, aerospace, and construction, must adhere to strict thickness measurement standards.
Common Methods for Measuring Coating Thickness
Different coatings and substrates require different measurement techniques. The choice of paint thickness measurement method depends on factors such as substrate material, coating type, and accuracy requirements. Below are the most widely used techniques:
1. Magnetic Methods (For Ferrous Substrates)
Magnetic gauges use the principle of magnetic attraction to measure the thickness of non-magnetic coatings on ferrous (iron and steel) substrates. These instruments include:
Magnetic Pull-Off Gauges – Measure coating thickness by assessing the force needed to pull a magnet from the coated surface.
Electromagnetic Induction Gauges – Provide high-precision, nondestructive measurement of paint thickness, powder coatings, and metal plating on ferrous substrates.
Industries Using Magnetic Methods: Automotive, shipbuilding, structural steel, and general industrial coatings.
2. Eddy Current Method (For Non-Ferrous Substrates)
Eddy current testing measures coating thickness on non-conductive coatings over non-ferrous metal substrates, such as aluminum, brass, and copper. The device generates an alternating electromagnetic field that interacts with the substrate to determine thickness.
Common Applications: Aerospace, electronics, aluminum anodizing, and powder coating industries.
3. Ultrasonic Coating Thickness Measurement
Ultrasonic gauges are used to measure coating thickness on non-metallic substrates, such as plastics, composites, wood, and concrete. They work by transmitting ultrasonic pulses through the coating and measuring the time it takes for them to reflect back from the substrate.
Key Advantages:
Ideal for thick coatings and multilayer applications.
Nondestructive and highly precise.
Useful for measuring coating thickness on irregular surfaces.
Industries Benefiting from Ultrasonic Testing: Marine, aerospace, industrial protective coatings, and construction.
4. Micrometer Measurement (Mechanical Thickness Testing)
Micrometers, also known as calipers, provide a simple yet effective method for coating thickness measurement by measuring total thickness before and after coating application.
Limitations:
Requires direct contact with the surface.
Not suitable for thin coatings or delicate finishes.
Best For: Thick coatings, powder coatings, and metal plating applications.
5. Destructive Testing (Cross-Sectioning & Gravimetric Methods)
When nondestructive methods aren’t viable, destructive testing techniques can be used to determine film thickness by cutting or removing a section of the coating and measuring it under a microscope.
Methods Include:
Cross-Sectioning – Cutting into the coating and analyzing thickness under magnification.
Gravimetric Measurement – Weighing the coated sample before and after stripping to determine the thickness.
When to Use Destructive Testing:
When extreme precision is required.
For research and development applications.
When working with high-performance coatings in aerospace and automotive industries.
Choosing the Right Coating Thickness Gauge
Selecting the right coating thickness measurement tool depends on various factors, such as:
Substrate Material – Magnetic methods for ferrous metals, eddy current for non-ferrous metals, and ultrasonic for non-metallic substrates.
Coating Type – Powder coatings, anodized layers, and protective films require specific measurement techniques.
Measurement Range & Accuracy – Consider the required precision and thickness range.
Industry Compliance – Ensure the device meets ISO, ASTM, and NIST traceability standards.
Innovative Coating Thickness Measurement Solutions
Advanced coating thickness measurement tools, such as those offered by Helmut Fischer , Elcometer , DeFelsko Corporation, provide high-accuracy, user-friendly, and durable solutions for various industries. Their products include:
Helmut Fischer:
Dualscope MPO – Versatile coating thickness gauge for both ferrous and non-ferrous metals.
DMP 20 & DMP 40 – Versatile coating thickness gauge for both ferrous and non-ferrous metals.
MMS INSPECTION DFT – Versatile coating thickness gauge for both ferrous and non-ferrous metals.
Phascope PMP 10- Versatile coating thickness gauge for both ferrous and non-ferrous metals , Zinc flake and Copper Coating.
ELCOMETER : (with one flagship model)
Elcometer 456 – Versatile coating thickness gauge for both ferrous and non-ferrous metals.
DeFelsko Corporation:
PosiTector 6000 – Versatile coating thickness gauge for both ferrous and non-ferrous metals.
PosiTector 200 – Ultrasonic gauge for measuring coatings on plastic, wood, and composites.
These tools help businesses maintain precision, efficiency, and compliance with industry standards while reducing material waste and costs.
Conclusion
Coating thickness measurement is vital for product quality, performance, and compliance. With numerous techniques available, choosing the right coating thickness gauge ensures accurate measurements, reduced waste, and optimal process control. Whether using magnetic induction, eddy current, ultrasonic, micrometer, or destructive testing methods, each approach serves specific industrial needs.
To find the best solution for your coating thickness measurement requirements, consider substrate type, coating material, precision needs, and industry regulations. Investing in advanced measurement tools helps businesses enhance efficiency, maintain compliance, and improve overall product reliability.
For industry-leading coating thickness measurement solutions, explore Nextagen Coating Thickness Range range of innovative products and software to achieve the highest standards of quality and accuracy.
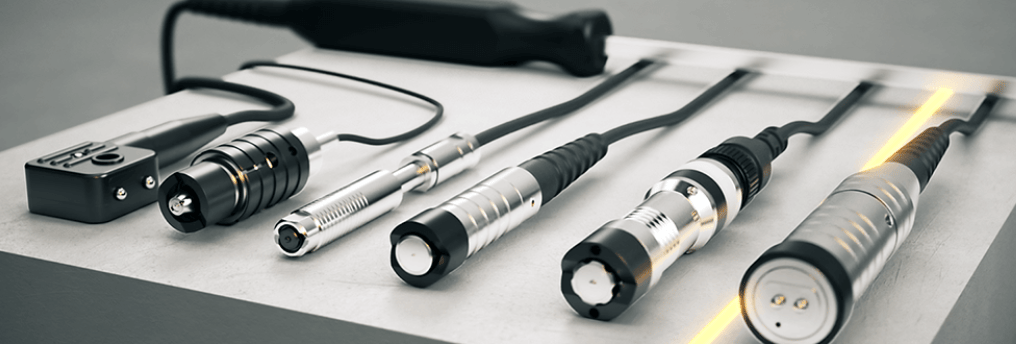
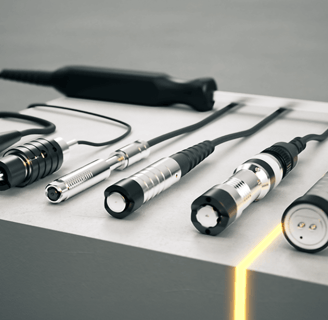
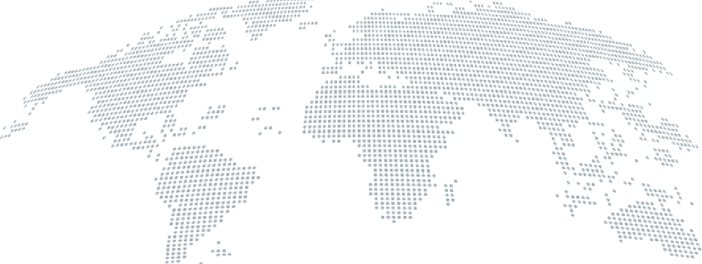
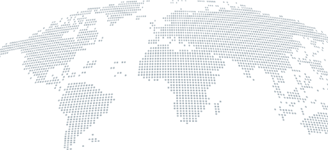
Innovation House
Mon-Sat 9am-7pm
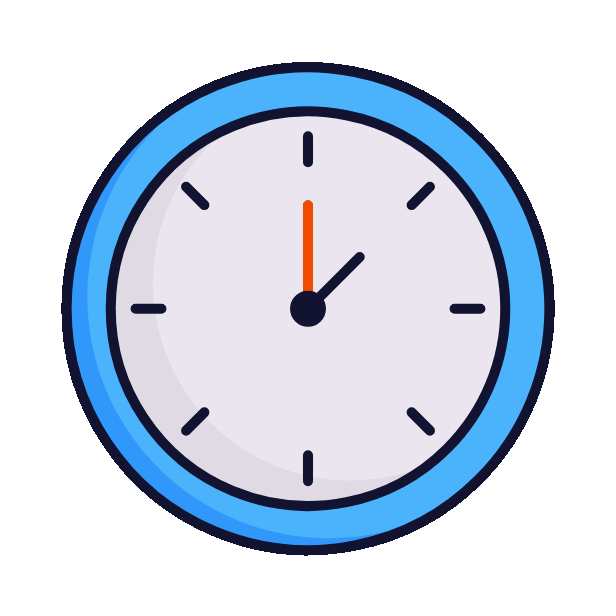
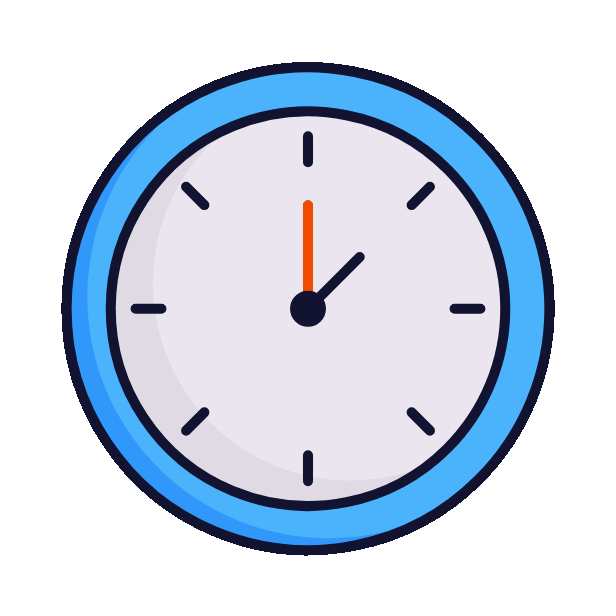
contact@nextagen.in


+91 2654059388
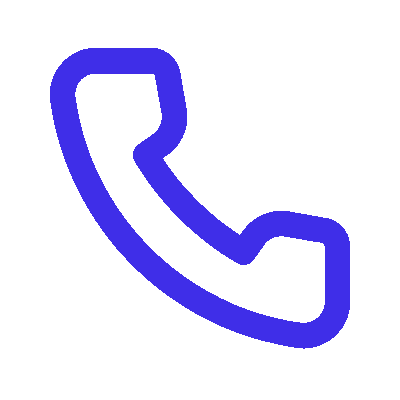
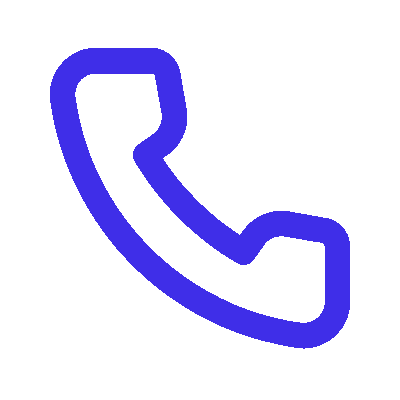
© 2024 Nextagen Analytics Private Limited . All Rights Reserved.