Hegman Gauge: Comprehensive Overview and Standards
Nextagen Analytics
2/4/20253 min read
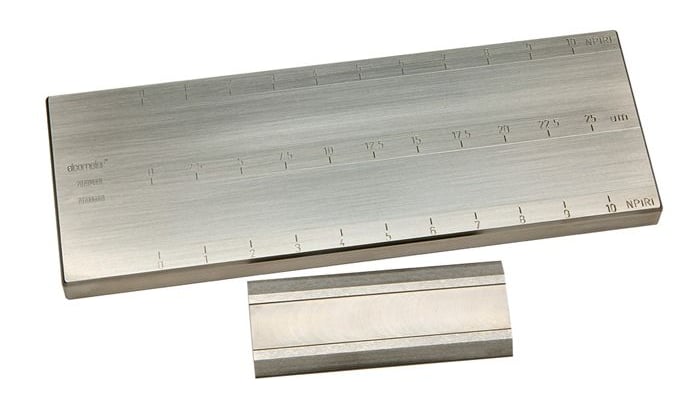
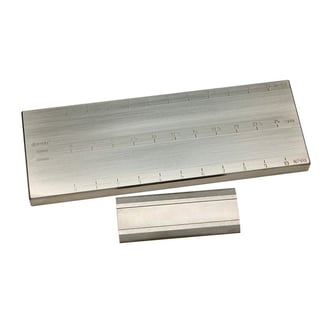
Introduction
The Hegman gauge, also known as a fineness of grind gauge, is a precision tool used to measure the particle size and dispersion quality of liquid and paste-based materials. These include paints, coatings, inks, cosmetics, and other suspensions. Ensuring the proper dispersion of particles in such applications is essential for maintaining product performance, aesthetics, and consistency.
History and Development
The gauge was developed in response to industry needs for a standardized method of evaluating grind quality. As manufacturing expanded, sectors such as paint and printing required finer particle dispersion for superior product results. The Hegman gauge emerged as a practical tool to help technicians and engineers achieve these goals.
Design and Working Principle
The Hegman gauge typically consists of a steel block with a tapered channel that runs from a deep end to a shallow end. This groove ranges from 0 microns at the shallow end to 100 microns at the deep end, with measurements typically provided on both the Hegman scale and in microns.
Key Features:
Constructed from high-grade stainless steel for durability.
Tapered groove measuring from 0 to 100 microns.
Dual measurement scales: Hegman and microns.
Precision flatness for accurate measurements.
How It Works:
A sample of the material is placed at the deep end of the groove.
A scraper spreads the material along the length of the channel.
The point at which particles become visible is noted on the scale.
This reading indicates the dispersion quality and particle size of the sample.
Hegman Scale Explanation
The Hegman scale provides a simple, standardized method to assess fineness. The scale ranges from 0 to 8:
0 Hegman: 100 microns (coarse particles)
8 Hegman: 0 microns (finest particles)
A higher Hegman reading indicates finer dispersion and better quality.
Applications Across Industries
The Hegman gauge is widely used in the following sectors:
Paints and Coatings: Ensures proper pigment dispersion for smooth finishes.
Printing Inks: Verifies particle fineness for clear and consistent prints.
Cosmetics: Confirms smooth formulation for creams, lotions, and powders.
Pharmaceuticals: Assists in maintaining consistency in suspensions.
Food Industry: Evaluates particle dispersion in sauces and pastes.
Standards Associated with Hegman Gauge Usage
Various international standards organizations have established guidelines for the use of Hegman gauges. These include ASTM, ISO, and DIN standards.
1. ASTM Standards:
ASTM D1210:
Title: Standard Test Method for Fineness of Dispersion of Pigment-Vehicle Systems by Hegman-Type Gage.
Purpose: Describes procedures to determine the fineness of grind for pigmented coatings.
Key Points: Specifies test conditions, sample preparation, and reporting requirements.
ASTM D333: Standard practice for dispersion testing of pigments in liquid media.
2. ISO Standards:
ISO 1524:
Title: Paints, varnishes, and printing inks — Determination of fineness of grind.
Purpose: Provides guidelines for testing particle size distribution using a grindometer.
Key Points: Establishes measurement protocols and reporting formats.
ISO 8780-2: Grinding processes for dispersion quality.
3. DIN Standards:
DIN 53203:
Title: Determination of fineness of grind.
Purpose: German standard defining procedures for evaluating pigment dispersion.
Key Points: Includes instructions on gauge usage and interpretation of results.
These standards ensure uniformity in measurement practices and help maintain product quality across different industries.
Usage Guidelines
Sample Placement: Place the test sample at the groove’s deep end.
Spreading: Use a scraper to evenly distribute the sample.
Observation: Identify the point where particles become visible.
Recording: Note the corresponding scale value.
Calibration and Maintenance
Proper calibration and maintenance are crucial for accurate results.
Calibration Tips:
Use certified calibration plates.
Verify flatness regularly.
Compare readings with a standard sample.
Maintenance Guidelines:
Clean the gauge thoroughly after each use.
Store in a protective case to avoid damage.
Handle the scraper with care to maintain flatness.
Troubleshooting and Best Practices
Inconsistent Results: Ensure sample homogeneity.
Gauge Damage: Replace damaged gauges immediately.
Operator Errors: Train personnel for consistent handling.
Conclusion
The Hegman gauge plays a critical role in ensuring product quality and consistency in various industries. By adhering to associated standards such as ASTM, ISO, and DIN, manufacturers can achieve reliable and repeatable results, contributing to superior product performance and customer satisfaction.
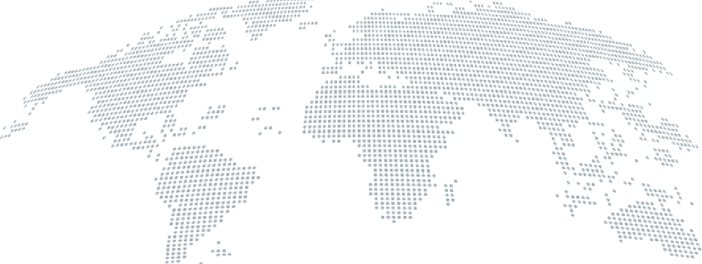
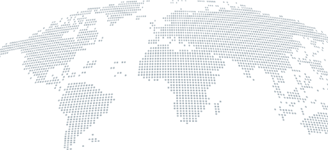
Innovation House
Mon-Sat 9am-7pm
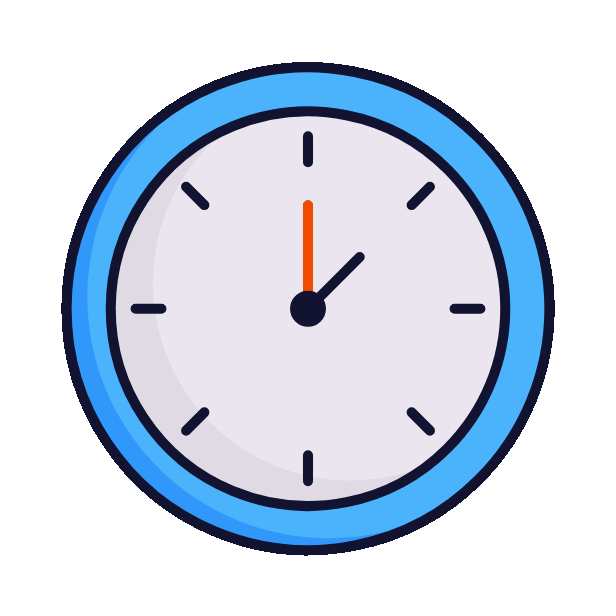
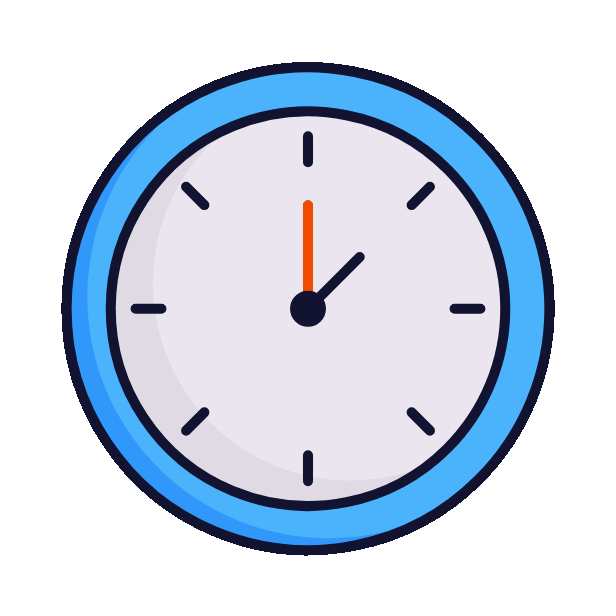
contact@nextagen.in


+91 2654059388
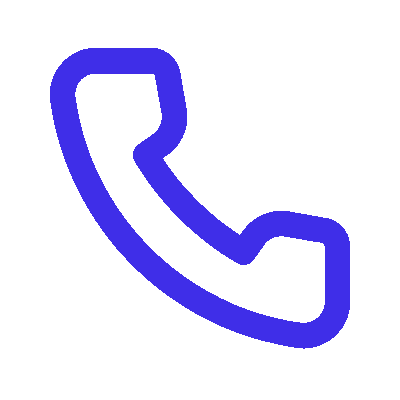
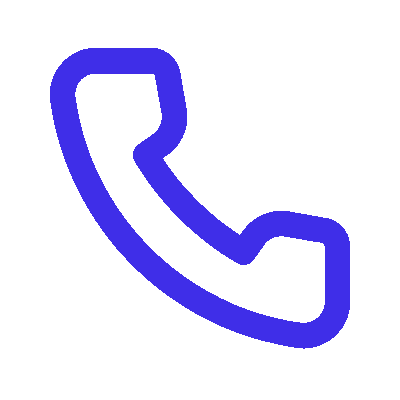
© 2024 Nextagen Analytics Private Limited . All Rights Reserved.