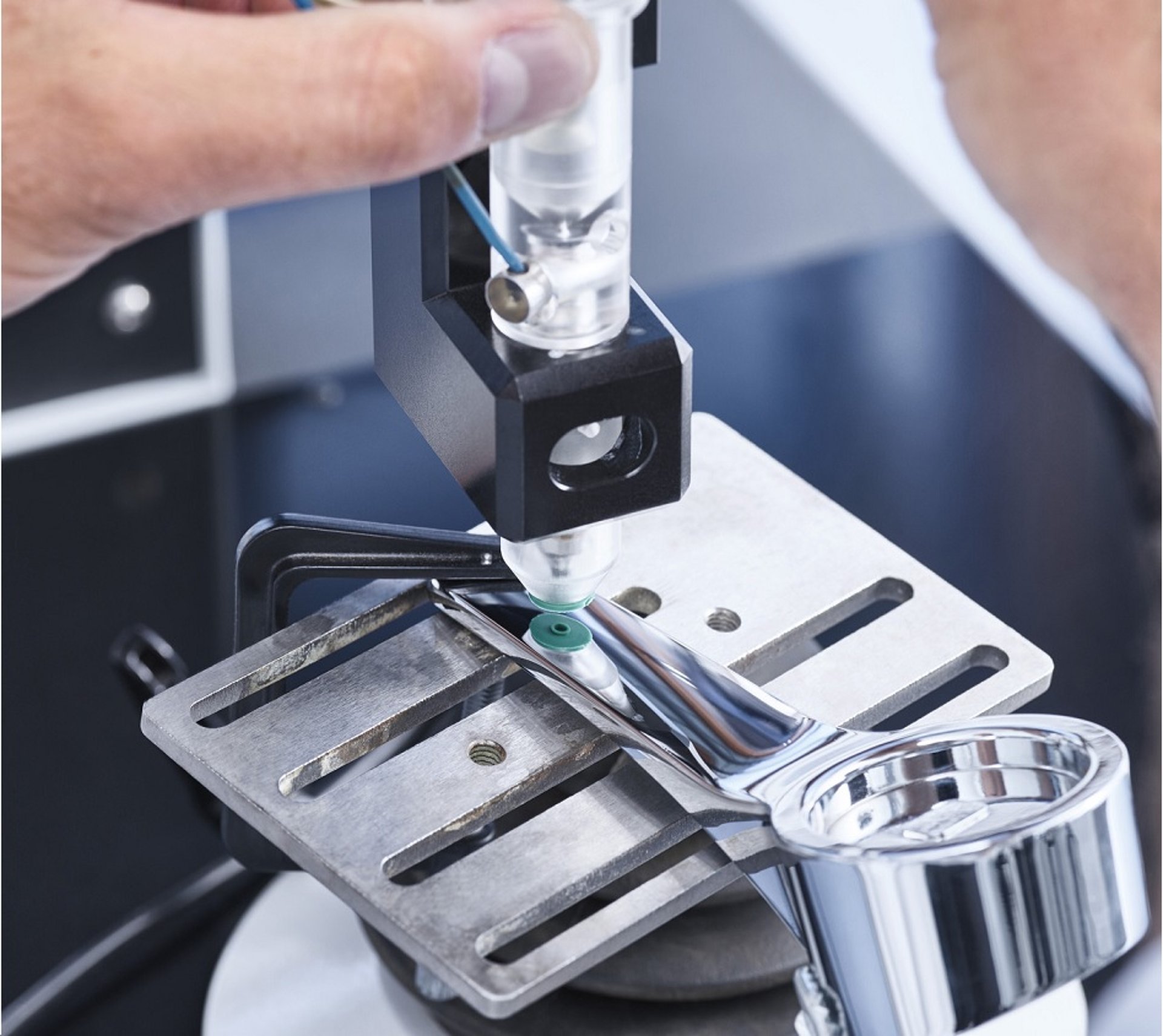
This is how coulometric method works.
Coulometry is the reverse of the galvanization process. In coulometric coating thickness measurement, a metal layer is dissolved by a constant electric current.
Measuring is carried out using a measuring cell filled with an electrolyte. This miniature bath is placed on the coating with the opening having a defined area. Due to the action of the electrolyte and the direct current, the metal atoms from the coating enter the solution as cations and migrate to the cathode of the measuring cell.
When the entire coating is detached and the electrolyte reaches the underlying material (base material or another layer), there is an increase in electrical resistance and thus a measurable voltage jump, which leads to an automatic end to the measurement.
From the time that the dissolution process has taken, the coating thickness can be calculated via Faraday's Law.
Where is this process used?
Metallic coatings (aluminum, copper, nickel, gold, silver) on different base materials
Electroplating coatings
Multilayer systems such as Cr/Ni/Cu on iron or plastic substrates (ABS)
Multiple nickel coatings (porous/bright/semi-bright) by means of step test
Applicable Standards
DIN EN ISO 2177
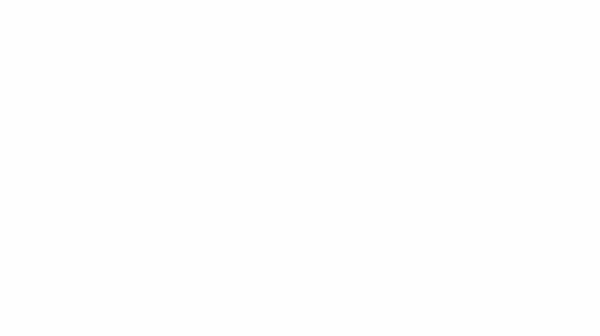
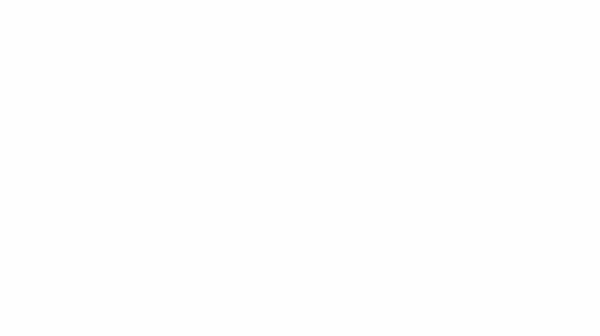
On the one hand, the composition of the electrolyte must match the base material and the coating to be dissolved. Secondly, the electrolyte can be consumed in the case of very thick coatings or during repeat measurements.
To keep error quantities to a minimum, contamination of the measuring point should be avoided. It is a good idea to lightly etch over the site before measuring to remove any oxide layers. If the measuring point is too close to the edge of the sample, edge effects can falsify the results. After measuring, it should also always be checked whether the layer has come off cleanly.
The measuring point should also be checked for leaks. If the measuring point is not flat or the measuring cell is used near some bends or curves, the electrolyte could leak out (even some drops), resulting in a larger resolution area and thus incorrect results.
Changes of the measuring point due to wear of the ring seal, changes of the contact pressure and other influences on the measuring point can cause measuring errors.
Measuring Point
Available Manufactures and Solutions
Helmut Fischer- Couloscope
Electrophysic- GalvanoTest
Kocour- 6000
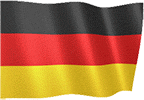
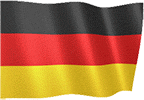
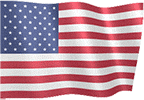
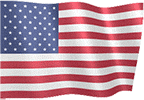
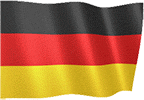
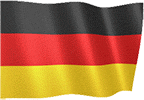
Kiran Electronics- Advance Micro Test
Technical comparison datasheet of manufacturers
Need application based assistance for brand and model selection
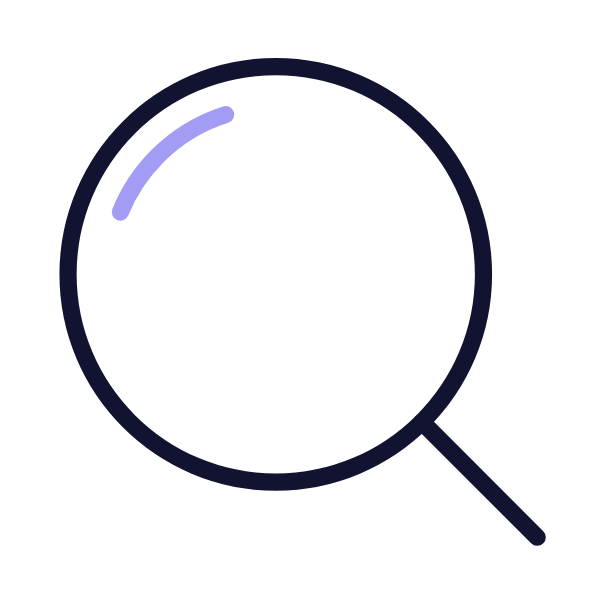
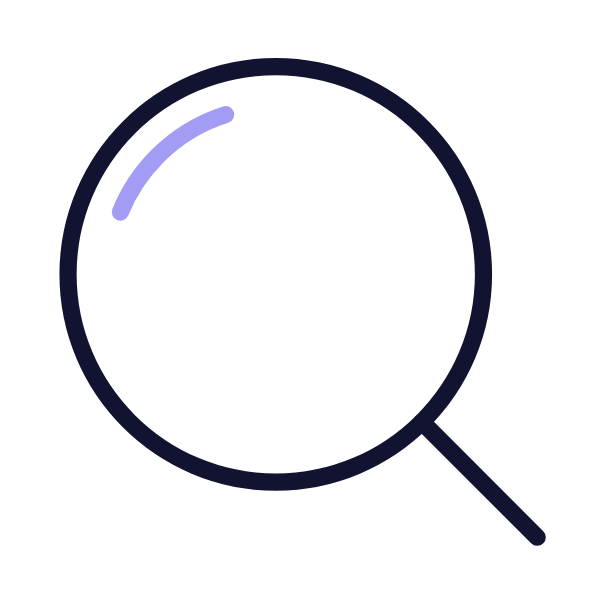
Need technical assistance to understand the technology
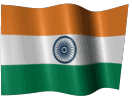
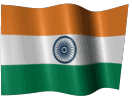
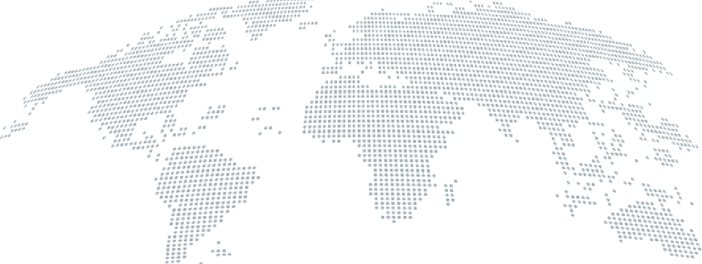
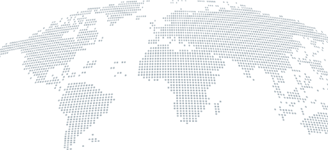
Innovation House
Mon-Sat 9am-7pm
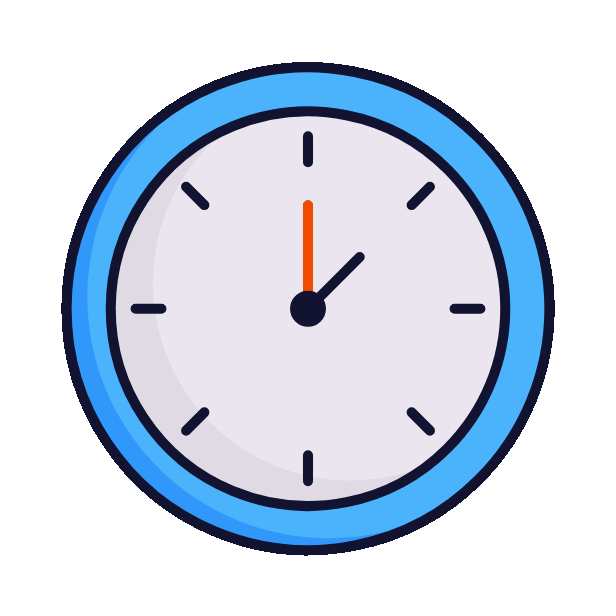
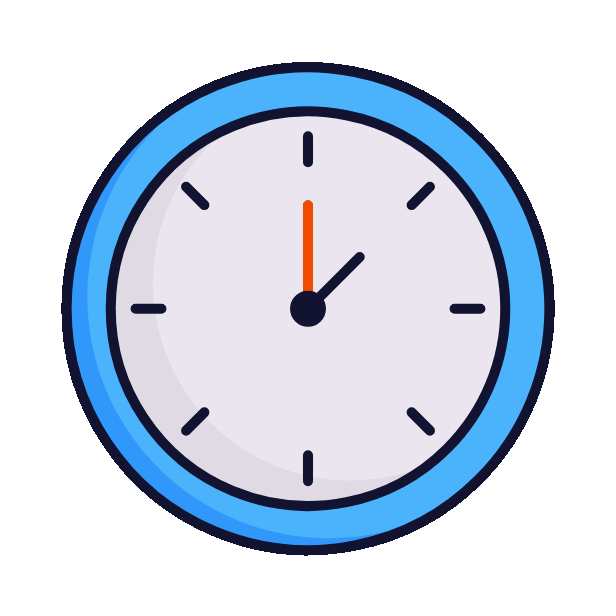
contact@nextagen.in


+91 2654059388
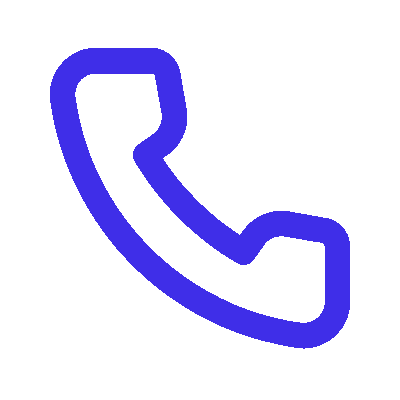
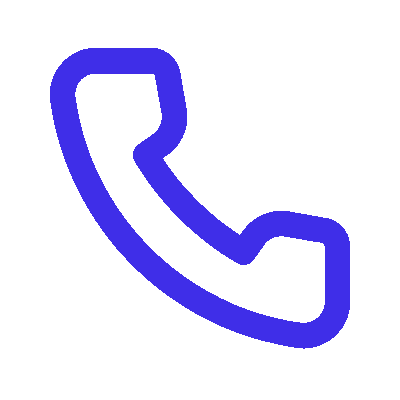
© 2024 Nextagen Analytics Private Limited . All Rights Reserved.